Design engineering studio
Discover our departments
Learn more about our individual departments. Any information is available here.
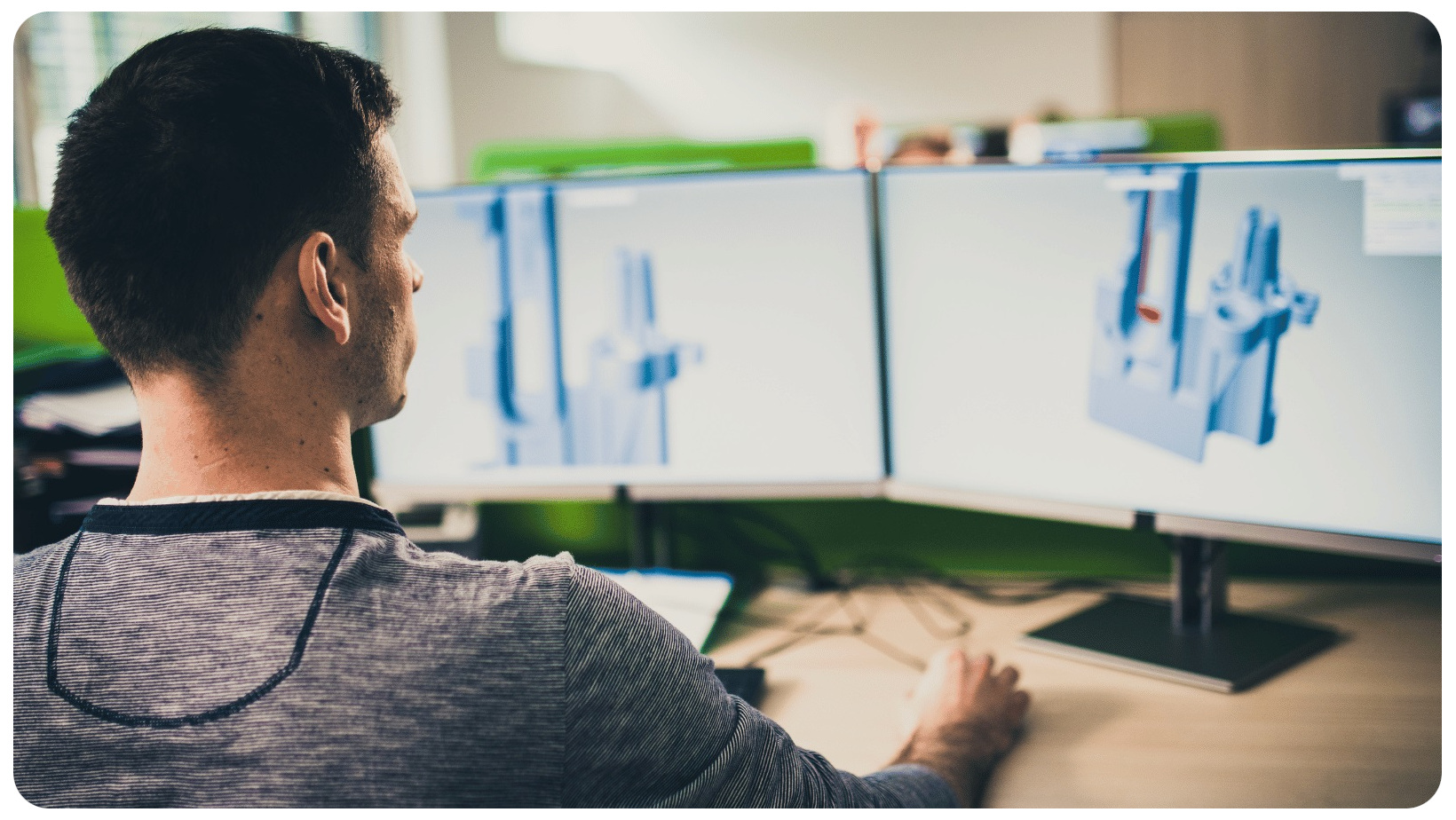
Design engineering studio
We provide you with our long-lasting experience in constructing injection moulds and state-of-the-art technologies for their fabrication. Our priority is to extend process-related knowledge. We are experienced and have the facilities and references in end-to-end support.
There are process engineers in the Design engineering studio who consult with the Customers and provide their support. To select the technology that meets Customer’s expectations, our process engineers consider the following product features:
- Predicted manufacturing quantities,
- Product operating environment,
- Material/plastic type,
- Certificates and standards,
- Accuracy and tolerance,
- Aesthetics.
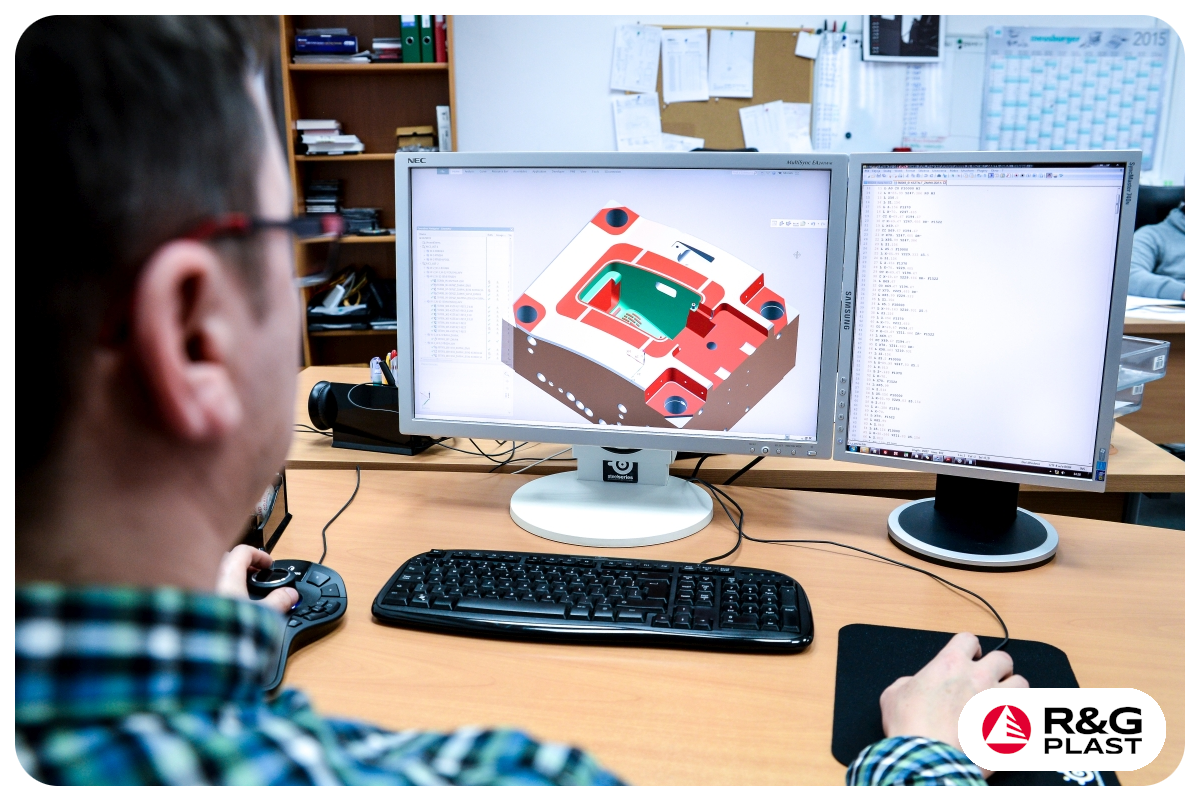
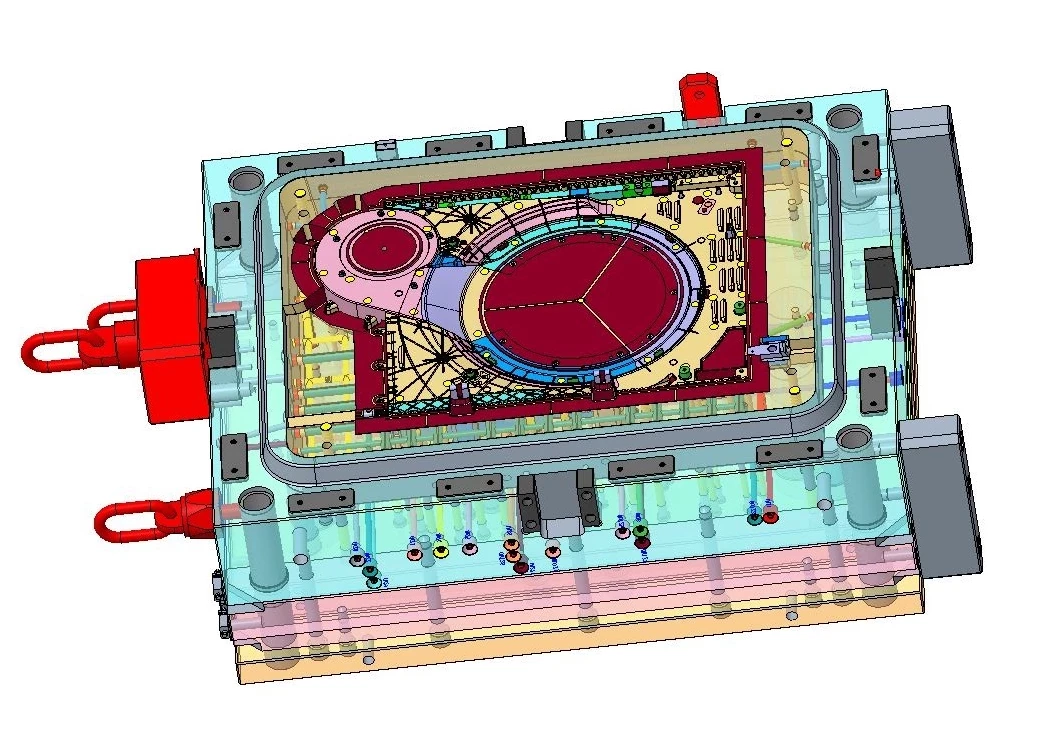
What we make?
We make tools on the basis of customer-provided technical files and a final product or 3D model delivered. We always try to suggest the best and, at the same time, the most affordable process solution.
We carry out the projects based on the documentation developed according to the latest CAD/CAM solutions. To develop the best possible solutions while designing moulds, we use CadMould to create simulations of the injection process.
To construct moulds, we use premium quality normalised Meusburger, FCPK Bytów, DME or HASCO components. We also work with Bohler Uddeholm and Multistal. – renown steel suppliers.
Production Stages
Stage I
We design a mould suitable for use at any type of injection moulding machine, create processes, help select the parameters of a plastic to manufacture from moulded pieces, and submit a price calculation including the costs of injection moulds and the manufacturing process before mould construction. Then we compile a complete documentation and grant a warranty for the entire solution.
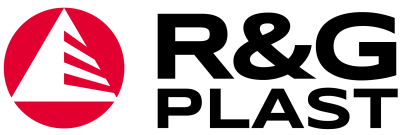
Stage II
The second stage involves the fabrication of individual components of the tool. Tool fabrication is a process characterised by continuous communication with the Customer. Continuous quality and tool fabrication control ensures an effective process of implementation of a new product – the effect is a high-quality final product.
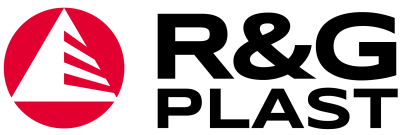
Stage III
The final strategic stage is manufacturing. We supervise the tool implementation from the moment it was designed to its fabrication, commissioning, and verification in continuous operating mode; all these actions are performed by our Quality Department personnel.
R&G PLAST’s construction studio is made up of qualified engineers who are at your disposal at every project stage.
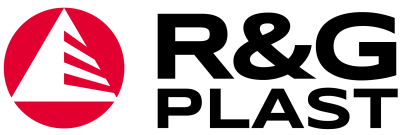
3D PRINTING
3D Printing
Our range of services includes prototyping a detail using a 3D printer. Our 3D printer is the best and most cutting-edge equipment that allows us to accurately reproduce 3D model dimensions and print components that require a high level of dimensional precision.
Prototyping a product at an early stage of design engineering brings many benefits: it facilitates the verification of functionality-related assumptions, improves the appearance, etc. Modifications introduced at an early process stage (before manufacturing) eliminate the need to make expensive changes in production tools. This method cannot be substituted even by the best visualisation.
We create prototypes on individual customer requests. 3D printing technology allows making a component at every design engineering stage and is a fast process that is incomparably cheaper in relation to traditional fabrication techniques.

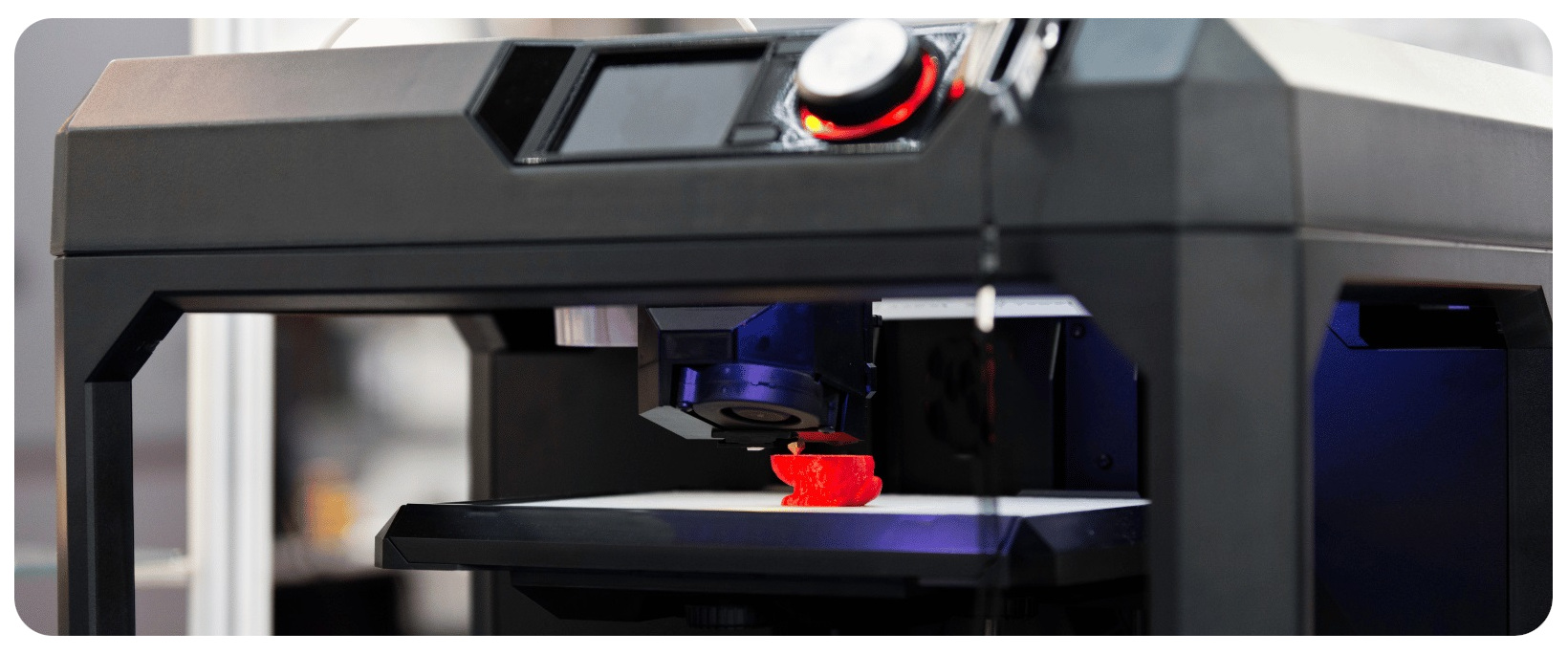
We provide:
- A design of a model (CAD-based).
- Making a component using a 3D printer based on our own or customer-provided 3D models.
- Immediate project performance.
- Premium quality prototypes.